INTEGRATED PRECISION BORE CLADDER
GET THE Precision AND SIMPLICITY YOU NEED
Our hotwire GTAW TIG cladding systems features a manipulator with precision column lift and precision boom motion and a motorized turntable. The precision manipulator motion eliminates the need to mount heavy motorized slides to the end of the boom for torch manipulation that is necessary for most conventional bore cladding systems. The two axes of manipulator motion are AVC controlled for vectored AVC.
The welding equipment is mounted to an equipment platform located on the backside of the column. This allows the manipulator to be more portable and compact.
The combination of the XM Controller and the precision horizontal, vertical, and rotary axes of motion provide a very powerful bore cladding system with a minimal footprint.
30+ Years of welding Automation Excellence
The AMET bore cladder is a compact yet versatile and complete bore cladding system. The TIG cladding systems include the following capabilities:
- Horizontal Motion: 78.7 in (2000 mm) of precision motorized boom motion
- Vertical Motion: 78.7 in (2000 mm) of precision motorized column (mast) motion
- Column Rotation: 360 degrees of manual rotation with manual brakes to maintain position.
- Turntable Weight: The turntable is capable of rotating parts up to 2,200 lb (1000 kg)
- Part Diameter: The turntable faceplate is capable of holding parts with an outer diameter (OD) up to 36 in (914 mm)
- Wire Feed Speed: Capable of programmable wire feed from 1 to 500 in/min (25 to 12700 mm/min)
- Hotwire Power Supply: 200 Amps up to 20 Volts
- Welding Power Supply: Output range of 5-350 Amps
- Water Circulator: Capable of cooling torches up to 500 Amps
- Water-cooled Bore Torch:
- Minimum Bore Diameter: 2.13 in (54 mm)
- Max Weld Current: 200 Amps at 100% duty-cycle
- Max Hotwire Current: 70 Amps
- Reach: 32 in (813 mm)
Additional features are available to increase the capabilities of this cladding system. Please see the Optional Features section for more information.
This completely automated hotwire GTAW cladding system provides several benefits over manual welding or non-automated welding systems.
- Precision rotation control of the turntable. The rotating motion is servo motor driven and controlled through the XM Controller. The turntable also includes a 500 Amp built-in ground.
- Precision vertical motion of the boom is provided by a servo motor driven lead screw drive along precision rails, which allows the smooth motion necessary for cladding operations.
- The horizontal motion of the boom is servo motor driven with a precision rack and pinion drive along machined rails.
- AVC (Arc Voltage Control) modules control both the horizontal and vertical axes to provide vectored AVC. These two linear axes are integrated together and each one takes continuous samples to maintain proper arc standoff. The AVC axes and the rotary axis are integrated together for programmable cladding of the bore wall.
- The system is designed to be compact and self-contained. The manipulator features an equipment platform mounted to the back side of the column, so the manipulator and the welding equipment are one unit. Moving the manipulator and equipment can be easily done with a forklift or overhead crane. This also minimizes trip hazards and clutter by consolidating cables and hoses to one location.
- The hotwire power supply significantly increases deposition rates over cold wire GTAW. Rates are closer to the deposition rates of GMAW but with cleaner higher-quality GTAW welds.
- Gas flow and water flow are monitored to help maintain high-quality welds and protect the bore torch from overheating.
XM Controller
The XM Controller is integrated into all of the major programmable components of the TIG cladding systems. The following axes of motion and components are integrated into the system:
- Welding power supply integration for controlling arc on/off and programmable current.
- Turntable Rotation: The XM and Rotary module integrate with the servo motor driven turntable to provide programmable motion with override capabilities. The rotation can be programmed by degrees, RPM, or time. Continuous and manual rotation are also possible using the XM interface.
- AVC Horizontal: The XM and an AVC module combine with the servo motor driven boom for automated control of the arc voltage. The arc standoff is automatically monitored and adjusted throughout the weld to ensure a constant and consistent voltage is maintained.
- AVC Vertical: The XM and an AVC module combine with the servo motor driven vertical column lift for automated control of the arc voltage. The AVCs of both the vertical and horizontal axes integrate together to provide vectored AVC. The arc voltage sensitivity settings are adjustable for both axes.
- Wire Feeder: AMET’s precision hotwire power supply with built-in wire feed module offers control over wire feed speed, wire retract, and current and voltage for hotwire feeding.
- Gas Control: Manual flow meters and a gas solenoid provide a constant gas flow rate. A soft button activates gas at the default flow rate until the button is deactivated or until the end of the weld program.
- Water Control: The water circulator on/off control as well as a sensor for detecting water flow are integrated into the XM. If no water flow is sensed, then an alert is displayed on the XM screen.
Testimonials
Great Partner
"AMET has been a great partner because they are appropriately positioned to act when we need a new solution engineered or need to service an existing solution. In the end the price of a solution is negligible if it works properly, and the vendor can keep it working through their service efforts. AMET knows these things and services their customers accordingly."
- Matrix Drilling Products
15+ Years
"For over 15 years now I have had the privilege of working with AMET. I have personally seen how AMET Inc. industry knowledge and engineering expertise has enabled my business to increase weld quality and production and allow our clients to improve the strength and durability of their products."
- G. Wright's Welding Ltd.
Exceptional Team
"AMET’s team is exceptional to work with. They look at the provided solution as a whole – from operator interfaces to engineering requirements, they seek to understand the customer’s needs throughout the project. This results in a welding system that is robust, embraced by the workforce, and meets the rigorous requirements of Blue Origin’s vehicles and engines. We’re excited to work with AMET on our vision of millions of people living and working in space."
- Blue Origin
1. The precision column lift is achieved through a servo motor driven lead screw drive along machined rails. Precision lifting of the boom provides the system with the necessary vertical motion for spiral or step index cladding. A flexible cable carrier is included to organize and protect the life of the cables during motion.
2. The precision boom drive features a servo motor driven rack and pinion drive along machined rails for horizontal motion of the bore torch. The precision drive is controlled and driven by an AVC (Arc Voltage Control) module for constant arc standoff during cladding. A flexible cable carrier is included to organize and protect the life of the cables during motion.
3. A 4-roll wire drive assembly that is driven by a servo motor with encoder feedback provides precision wire delivery. Wire feed speed, start delay, and wire retract are each programmable with the XM Controller. The wire feeder offers high-precision wire delivery with an accuracy of +/- 1% of the programmed speed. The wire feeder also includes a manual hotwire nozzle positioner that is mounted to the torch.
4. The AMET bore torch is water-cooled and equipped with the necessary components for hotwire feeding. The torch is rated at 200 Amps at 100 percent duty-cycle.
5. The included turn table is capable of continuous rotation for cladding the entire part without stopping. The rotating motion is controllable and programmable through the XM Controller.
6. AMET’s precision hotwire power supply preheats the wire prior to entering the weld puddle, which increases wire deposition over a cold wire GTAW system. The preheating of the welding wire also provides a cleaning effect, which improves the quality of the weld puddle. The current and voltage are adjustable up to 200 Amps and 20 Volts respectively.
7. A 350 Amp DC GTAW welding power supply is integrated into the system for programmable control of the weld parameters. The power supply is capable of cladding with a wide range of filler metals including hard metals like Inconel.
8. A 500 Amp water circulator is integrated into the system to prevent the weld torch from overheating.
9. A single point power distribution cabinet is included that provides fuse-protected power to the entire system from a single primary power circuit (provided by client).
ADDITIONAL MANIPULATOR TRAVEL
An additional 24 in (610 mm) of precision travel can be added to either the vertical or horizontal travel axes of the manipulator. These additional capacities increase the work envelope so larger parts can be clad than with the standard version.
LARGER TURNTABLE
AMET’s turntables are available with larger weight capacities.
5,525 lb (2500 kg)
11,000 lb (5000 kg)
22,100 lb (10000 kg)
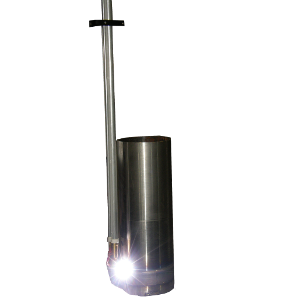
LARGER BORE TORCH
AMET’s compact bore torch is included with this system. AMET’s standard bore torch is available for medium sized bores. With this larger torch, the minimum bore diameter is increased to 3.5 in (89 mm). The standard bore torch length is about 48 in (1219 mm) as opposed to the standard 36 in (914 mm) of the compact torch.
OFFLINE PROGRAMMING SOFTWARE
Weld programs can be created, modified, or stored on a PC. These programs can be moved back and forth between the controller and the PC using a USB storage device or through an Ethernet connection. This software can increase productivity by allowing programs to be created/edited while the weld controller is executing another weld program.
GRIPPERS AND CHUCKS
A variety of optional part holding devices may be added to standard faceplates. These include grippers, three jaw scroll chucks, three jaw pneumatic chucks as well as other part holding solutions.
INTERSECTING BORE CLADDING CAPABILITY
Intersecting bore location and size can be programmed through the XM® or XPro Controller. During cladding, the arc will automatically be extinguished when the torch reaches the edge of the intersecting bore and then reignite once it reaches the other side. This will be repeated until the system has clad around the entire intersecting bore and then continuous cladding will resume. Bores must intersect the main part at an angle perpendicular to the center.
ARC VIEWING CAMERA
Arc Viewing Cameras can be added to a GTAW/PAW system giving the operator a view of the weld arc from a remote location. This keeps the operator in a safe location and reduces operator stress and fatigue. Additionally, the image that is shown on the monitor is magnified and shows greater detail than what could be observed without the camera. Multiple cameras may be integrated for projects where a view of the lead and trail side of the weld zone is required. Please see the Arc Viewing Camera page for additional information.
COMPLEX INTERSECTING BORE CLADDING
Includes all of the features from the Intersecting Bore Cladding option with the addition of automatically cladding bores at off-center and off-angle intersections.
GAS VALVES
Valves used in the oil and gas industry often require corrosive resistant coatings on sections of the inner diameter or along the entire length. Bore cladders are used to apply the corrosive resistant metals to the ID of valves.
BLOWOUT PREVENTER
Blowout preventers require corrosion-resistant overlays of the bores and components to ensure they can withstand harsh oil and gas environments. Our systems and controls provide an excellent solution for BOPs whether your company is the primary manufacturer or performs repairs.
INTERSECTING BORES
Parts with intersecting bores can be welded with AMET’s welding systems. This is facilitated by our use of intelligent software matched with premium hardware.
BALL VALVES
Ball valves require corrosion-resistant overlay for use in the oil and gas industry. Our systems are programmable to automatically clad around the opening of the ball for a completely automated solution.
Useful Links and Information:
Links
Related Products
Contact
Please call, write, or email our headquarters in Rexburg, Idaho for more information on how we can better serve you.
355 Dividend Dr
Rexburg, ID 83440